Corrective and Preventive Action Format | CAPA with Example
Last updated on November 16th, 2024 at 08:34 am
Corrective and Preventive Action Format | Download CAPA Format:
Corrective and Preventive Action Format with an example is illustrated below. CAPA has generally eliminated the causes of nonconformity. It is usually a set of actions i.e corrective action and preventive action, An Action to eliminate the Root cause of Non-conformity is called corrective action, and an action to eliminate the potential cause of non-conformity is called Preventive action.
Download CAPA Format / Template.
Free Download QMS & EHS Template/Format.
Download Corrective Action Format
You could like to read the below post:
why why analysis methodology | 5-why analysis step by step guide.
Free Download (QA, QC & 7-QC Tools Template /Format /form).
If you would like to learn more details on the CAPA Process & CAPA manufacturing example then read two important articles;
Corrective and Preventive Action (CAPA):
After knowing the symptom of the Problems why-why analysis plays a major part in identifying the root cause of the symptom of the problem.
In Industry CAPA is used to bring about improvement in process operation and to eliminate the causes of Problems. Corrective and preventive action is also a part of the Quality management system. CAPA is fully followed by the PDCA cycle for the implementation of the action plan and for monitoring the effectiveness of the action plan.
Corrective action implemented w.r.t the Customer Return, field failure, Manufacturing Process defects, warranty failure, Product design failure, server failure, etc.
Preventive action is implemented in reaction to identifying the potential cause of nonconformity. Common preventive actions in industries are given below, but are not limited to:
- Process/ potential failure Mode and Effects Analysis.
- Design Failure mode and effects analysis
- Quality Assurance Plan/ Control Plan
- Standard Operating Procedure / Work Instruction.
- Error Proofing/ Poka-yoke/ Mistake Proofing
- Reaction plan
- Risk mitigation plan
- Alarms System
- Process Validation
- Product validation
- Process layout.
- Process feasibility study
- Education and Training (Class Room / On-job-Training)
- Preventive maintenance.
Corrective Action vs Preventive Action:
Correction | Corrective Action | Preventive Action |
Action to eliminate the symptoms of problems. | Action to eliminate the root cause of nonconformity in order to prevent the recurrence. The action to be taken in order to eliminate the root cause. | Action to eliminate the potential causes of non-conformity in order to prevent their occurrence. To eliminate the potential cause of problems. The action to be taken in order to avoid root cause recurrence. |
For example -e.g.1- Quality Incident: Shrinkage in Automobile casting parts, Correction: Segregation of casting and if applicable, take approval from the customer for rework otherwise booked as a non-conforming product. | In example 1, the Root cause of shrinkage was the high pouring temperature, so the action to keep the pouring temperature within the specification is the Corrective action. | In example 1, Periodic monitoring of the pouring temperature with the help of a check sheet or control chart, etc. |
E.g.2-EHS Incident: Water spillage from the pipeline, Correction-close the water valve of the pipeline to avoid the water spillage. | In e.g2- The Water spillage incident happened due to the damage to the pipeline. So Repairing the pipeline is the corrective action | In example 2, Periodic checking of the condition of the pipeline or PM of pipeline. |
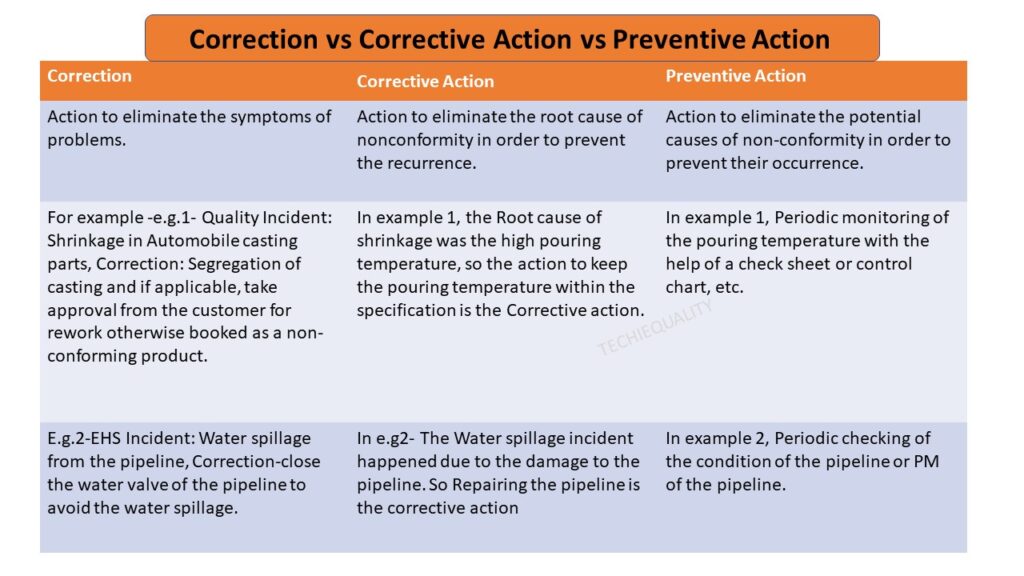
Corrective and Preventive Action Format / CAPA Format / CAPA Template in Word
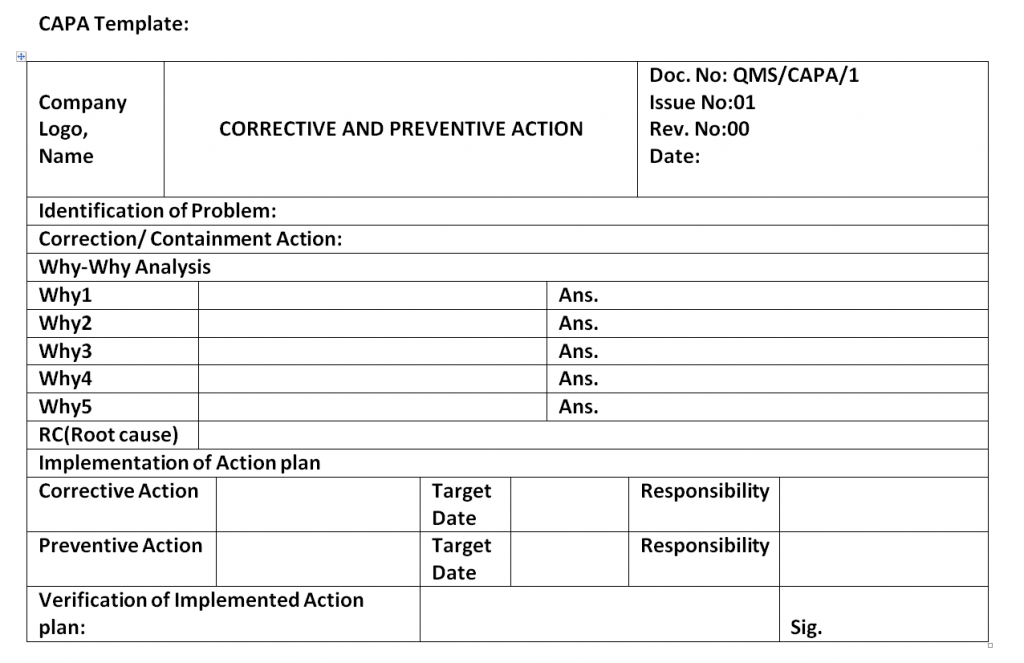
Use our approved simple & best formats or templates in your organization/ manufacturing units and provide us with your valuable feedback. DOWNLOAD-Template/ Format of 7QC tools, Cp & Cpk Calculation Sheet, FTA, 5W2H, 5W1H, SWOT Analysis format, Run Chart, 8D Format, Control Chart, OEE calculation excel sheet, CAPA Word format /Template, etc.
CAPA Format in Excel
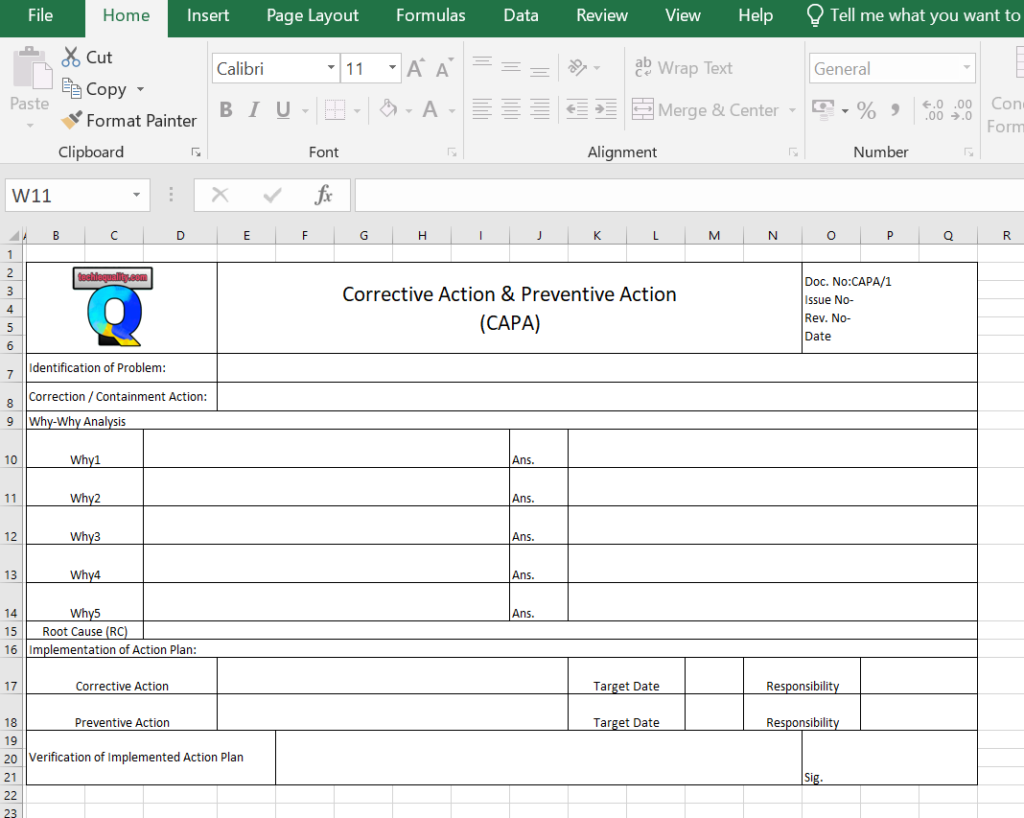
Corrective and Preventive Action Format filled up Example-1 :
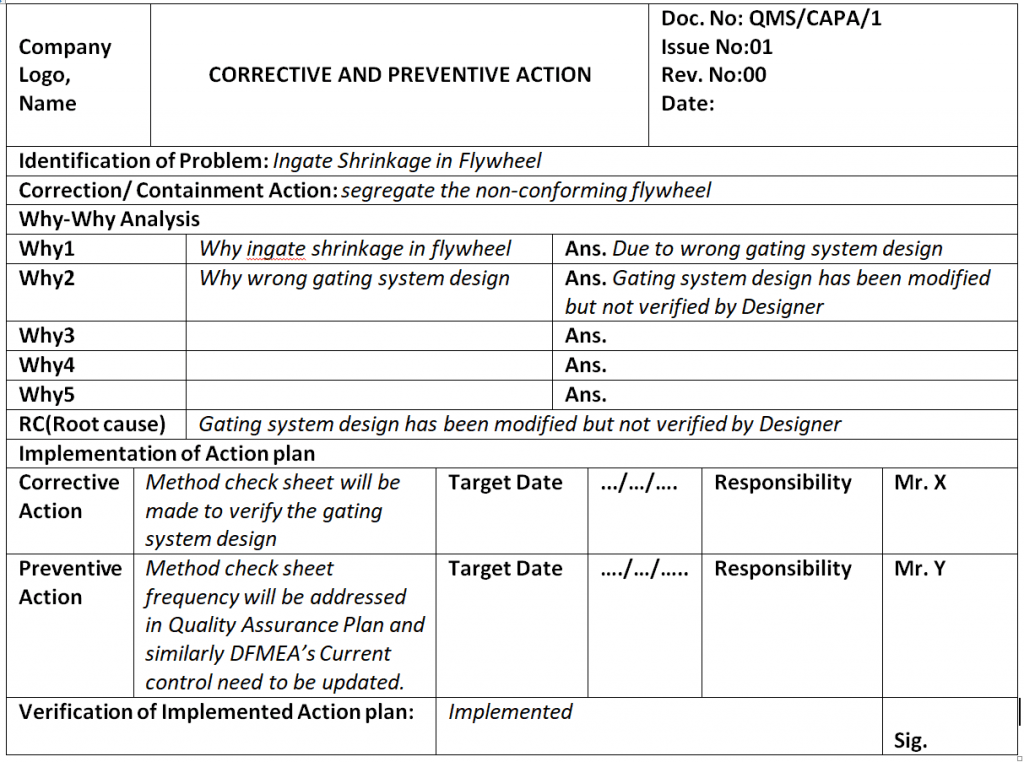
EXAMPLE-1: Shrinkage Defect
Identification of Problem: Ingate Shrinkage in Flywheel…
Correction/ Containment Action: segregate the non-conforming flywheel.
Why-1 | Why Ingate shrinkage in a flywheel | Ans. Due to the wrong gating system design |
Why-2 | Why the wrong gating system design | Ans. The gating system design has been modified but not verified by the Designer |
RC(Root cause): The gating system design has been modified but not verified by the Designer |
Implementation of the Action plan:
Corrective Action | A method check sheet will be made to verify the gating system design | Target Date | xx/yy/2020 | Responsibility | Mr.Z |
Preventive Action | Method check sheet frequency will be addressed in the Quality Assurance Plan and similarly, DFMEAās Current control needs to be updated. | Target Date | xx/yy/2020 | Responsibility | Mr.Z |
Verification of Implemented Action Plan: Implemented. |
EXAMPLE-2:
Details description of Example-2 (CAPA of Fire Incidents):
Identification of Problem: Fire incident.
Correction/ Containment Action: Put out the fire.
Why-Why Analysis of Fire Incident.
Why-1 | Why fire incidents occurred? | Ans. Due to LPG leakage from the supply pipelineās valve |
Why-2 | Why LPG leakage from the supply pipelineās valve? | Ans. Due to a corroded /rusted valve |
Why-3 | Why is the valve corroded /rusted? | Ans. Maintenance of the pipeline has not been done timely |
Why-4 | Why maintenance of the pipeline has not been done timely? | Ans. Because the maintenance schedule is not followed as per plan. |
Why-5 | Why maintenance schedule is not followed as per the plan? | Ans. The schedule was not comprehensive w.r.t criticality & availability of m/c, equipment, etc. |
RC (Root cause): The maintenance Schedule was not comprehensive.
Implementation of the Action Plan:
Corrective Action: A comprehensive maintenance schedule will be prepared w.r.t criticality & availability of m/c, equipment, device, etc. | Responsibility: Mr. XYZ (Maintenance Engineer) |
Preventive Action: Fortnightly adherence review of maintenance schedule by Mnt. Manager. | Responsibility: Mr. PQR (Maintenance Manager) |
Verification of Implemented Action plan: Implemented
Filled up CAPA Format in Word:
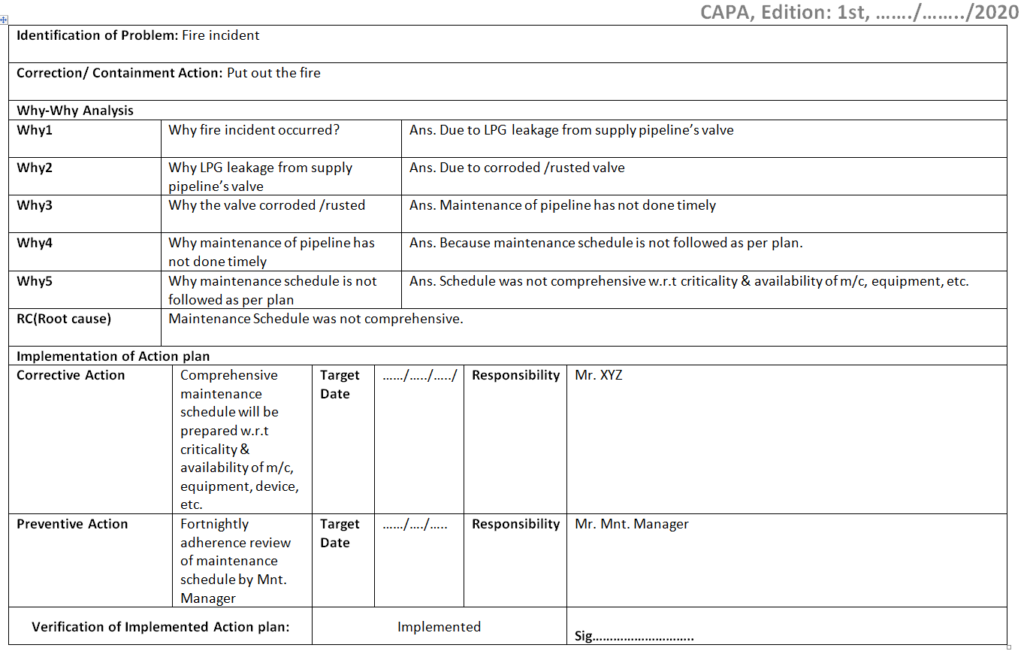
EXAMPLE-3:
In this example-3, we will discuss the latest type of format or template of CAPA, as you know the preventive action part does not exist in ISO 9001:2015 standard, and the same was replaced by Risk, so we have to analyze the risk instead of preventive action. Hence considering with new ISO 9001:2015 standard we have prepared a new format/template called the Corrective action & risk analysis template and illustrated the same with simple examples.
CORRECTIVE ACTION & RISK ANALYSIS TEMPLATE
How to fill up the CARA Template /Format? (Illustrated with example):
Problem Statement: Body fracture due to falling from an overhead water tank during construction work.
Correction: Medical treatment of the Patient and temporary seal of the construction area to stop the work and inspect the reason for the problem.
Root Cause Analysis:
We have done the root cause analysis given below using the 5Whys tools.
Why-Why Analysis:
Why-1 | Why body fracture? | Ans. Due to falling from an overhead water tank during construction work |
Why-2 | Why worker fell from an overhead water tank during construction work? | Ans. Due to slippage of the leg but the safety harness was not properly fitted |
Why-3 | Why the safety harness was not properly fitted? | Ans. The condition and fitment of the safety harness were not checked properly at an initial time before starting the work. |
Why-4 | Why Condition and fitment of the safety harness were not checked properly at the initial time before starting the work? | Ans. Due to a lack of knowledge and awareness |
Why-5 | Why lack of knowledge and awareness? | Ans. Periodically technical on-job training and awareness training is not conducted |
RC (Root cause): Periodically technical on-job training and awareness training are not conducted
Corrective Action & Risk Analysis:
Corrective Action: Technical on-job training and awareness training will be conducted weekly. Resp: – Mr.dddd, Trg. Date:ā¦/ā¦./ā¦.. | Risk /Issue: 1. Lack of technical knowledge & awareness. 2. Refresh training is not conducted. 3. The Condition of the safety harness is not checked from time to time. Etc. | Control Mechanism: 1 &2- Periodic training. 3. Weekly condition checking of safety harnesses. |
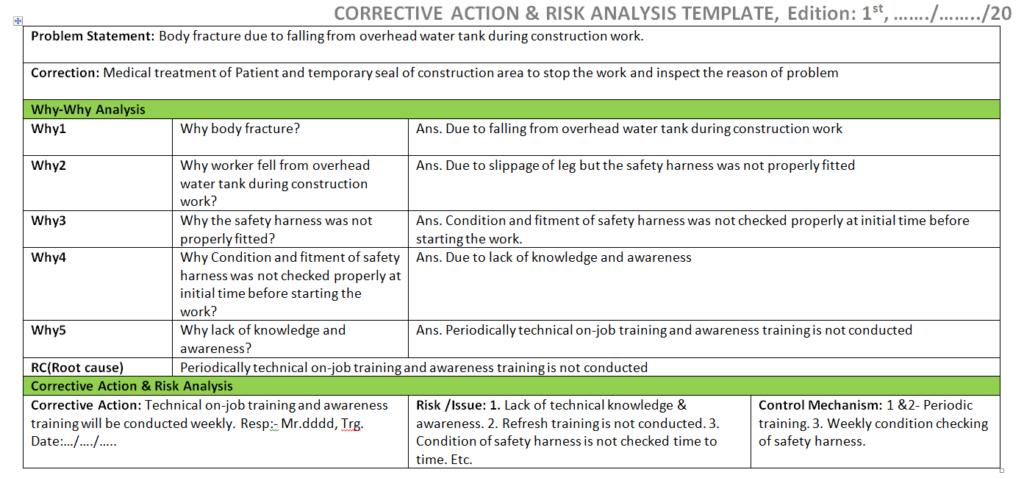
Example-4:
Here, we are going to discuss one example related to an accident and consider the same scenario for CAPA analysis. let’s say an accident occurred at a manufacturing unit while a man operating a machine. A CFT has been formed to analyze the accident and they prepared the CAPA report, which is mentioned below;
Correction: Medical treatment was provided to the patient and temporarily barricade the zone and machine for inspection purposes.
Root Cause: Lack of awareness
Corrective Action: Awareness training shall be provided to operators/workers
Preventive Action: Periodically awareness training needs shall be identified and the same to be imparted to concerned personnel.
FAQ1:
- What ISO 9001:2015 Said about CAPA?
- Ans: As you know the new ISO 9001:2015 standard asked about Correction, Corrective Action, and Risk & its mitigation plan. but not asked for preventive action. same mentioned in clause no.10.2 Nonconformity and corrective action in ISO 9001:2015 Standard. and for retained documented information, ISO 9001 asked for mandatory requirements as evidence of 1] the nature of the nonconformity and any subsequent actions taken. 2] the results of any corrective action.
- What IATF 16949:2016 Said about CAPA?
- Ans: The new IATF 16949 standard asked for Corrective action, Preventive action, and risk. In clause no 6.1.2.1, it’s said about Risk analysis, In 6.1.2.2-Preventive action and clause no. 10.2-Nonconformity & Corrective Action. After the incorporation of risk analysis in the IATF 16949 standard, still preventive action exists there.
FAQ2:
- What is CAPA?
- Ans: The full form of CAPA is Corrective Action & Preventive Action. corrective action eliminates the root cause of a non-conformity and PA eliminates the cause of potential non-conformity.
- How to write corrective and preventive action reports?
- Ans: We have already described at the top of this post with an example, simply go through it. Anyway, the most important part is the Root cause analysis and Why-Why analysis. Once you follow the right step to complete the RCA then, it will be very easy to write the CAPA in CAPA format /report, but in the new ISO 9001:2015 standard the preventive action has been replaced by Risk analysis, so when you write the CAPA, you have to cover the correction /containment action, corrective action then, you are supposed to identify the risk.
How to fill up the CAPA format quickly?
follow the below steps to fill up the CAPA format/template quickly;
- Identify the problem.
- Take containment action
- Do the RCA.
- Implement the CA & PA.
- Do the document changes
- Monitor the effectiveness
Corrective and Preventive action as per ISO 9001:2015 & IATF 16949:2016
CAPA (ISO 9001 v/s IATF 16949):
ISO 9001:2015 | IATF 16949:2016 | |
Corrective Action | Exist in the new standard | Exist |
Preventive Action | Not Exist, replaced by Risk analysis | Exist |
Risk Analysis | New Requirement | New Requirement |
QA/QC/TQM/Lean/6-Sigma Template or Format: