What is Preventive Maintenance? | Predictive Maintenance |Types & Example
What is Preventive Maintenance? | Predictive Maintenance |Types & Example:
Hi readers! Here, we are going to describe the concept of maintenance, types, examples, etc., basically, in this article, we will give more focus on what is preventive maintenance. Predictive maintenance and manufacturing examples and also on how to start a different type of maintenance activities in manufacturing industries. In manufacturing industries, we know very well how important the machine/ equipment’s condition get optimum productivity. Machines are subject to deterioration due to their use and exposure to environmental conditions. So, to maintain the machine condition we may need to carry out the maintenance of machines and equipment. The main purposes of maintenance are;
- To keep the operation in an optimum working condition.
- To increase the up-time of the machine.
- Less expenditure on repairs.
- To reduce the break-down percentage.
- To reduce the MTTR Value and increase the MTBF value.
- Lesser overtime pay for maintenance personnel.
- Increases productivity and minimizes waste and increases the rate of quality.
- To meet the time schedule of product delivery to customers.
- Reduces the downtime of the machines.
- To reduce the cost of downtime, it means when your machine’s downtime will be reduced then the idle time of the machine, workers, etc. will remain reduced and the respective cost as well. And others cost shall be reduced like scrap cost, rework cost, repair cost, maintenance labour, and overhead cost, etc.
- To prolong the useful life of the machine and equipment.
- To provide a condition of the machine that would permit their operation in the manner required for the process and without interruption to plans involving their use.
Maintenance:
We have already mentioned above the benefits of maintenance that why it is important in manufacturing industries, but anyway it is classified into many types based on different and different factors/ rules /operations, etc. Like [1] Mechanical maintenance, [2] Utility maintenance, [3] Electrical maintenance, [4] Machine maintenance, [5] Tool maintenance, etc. And similarly, it is also classified into different types like Preventive maintenance, Predictive maintenance, Breakdown Maintenance, Capital replacement, Planned maintenance, Schedule maintenance, and Corrective maintenance. Etc.
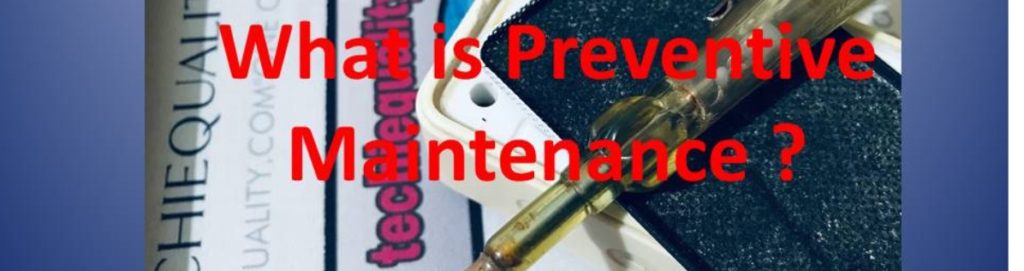
What is Preventive Maintenance?
Preventive maintenance is routine / time-based maintenance where actions are taken in a planned manner to prevent the breakdown of the machine. The main aim is to find out the problem and to fix it before it creates an issue. Generally, in industries, the common popular types of maintenance are used as [1] Preventive and, [2] Predictive maintenance. And also some industries followed and implemented the TPM activities.
Advantages of PM (Preventive Maintenance):
- Prolongs asset lifespans.
- Increased productivity and production.
- Greater safety of the workforce.
- Reduces the breakdown and increases the MTBF time.
- Reduce the scraps, rejection, and rework of products.
- Lower repair and maintenance costs, etc.
How to start or deploy Preventive Maintenance in Manufacturing Industries?
I am going to share my own experience here, whatever I have learned from a decade of time. Both preventive and predictive maintenance is a useful activity in manufacturing industries. So, if you would like to start Preventive maintenance in your organization then, just follow the below steps.
Step-1:
Go through the past data of breakdown process-wise / area-wise, then workstation-wise, and finally machine-wise. And also carefully read the machine manual, drawing, and related documents to understand the machine function, lubrication system, hydraulic system, etc.
Step-2:
Prepare the fishbone/cause & effect / Ishikawa Diagram of all failures.
Step-3:
Prepare the Standard Operating Procedure.
Step-4:
Prepare the Preventive maintenance check sheet / Checklist.
Step-5:
Prepare the activity road map including the responsibility for each and every activity, plan, and schedule.
Step-6:
Implement the road map, SOP, plan, schedule, and do checking w.r.t check sheet/checklist.
Step-7:
Analyze the data and take the action.
Step-8:
Review and update the documents like SOP, and check-sheet.
Step-9:
If applicable, do the horizontal deployment.
Example:
We have decided to start the Preventive maintenance of Process-1, Process-2, and Process-3, So accordingly both plan and schedule have been prepared.
Preventive Maintenance Plan of Process-1, having total 4 machines, M1, M2, M3 & M4.
Month | Week-1 | Week-2 | Week-3 | Week-4 |
Jan. | M1 | M2 | M4 | M3 |
Feb. | M3 | M1 | M2 | M4 |
Mar. | M3 | M4 | M1 | M2 |
Apr. | M4 | M3 | M2 | M1 |
May. | M3 | M2 | M1 | M4 |
Jun. | M2 | M1 | M4 | M3 |
Jul. | M1 | M2 | M3 | M4 |
Aug. | M4 | M1 | M2 | M3 |
Sep. | M3 | M4 | M1 | M2 |
Oct. | M4 | M3 | M2 | M1 |
Nov. | M3 | M2 | M1 | M4 |
Dec. | M2 | M1 | M4 | M3 |
After consultation with the production department and considering machine availability Sr. Maintenance Engineer has prepared the Preventive maintenance schedule and carried it out accordingly.
PM Schedule for the Month of Jan’yyyy.
M/C | Week-1 | Week-2 | Week-3 | Week-4 |
M1-Plan | 4.4.yy /Sunday | |||
Actual | ||||
M2-Plan | 11.4.yy/Sunday | |||
Actual | ||||
M4-Plan | 18.4.yy/Sunday | |||
Actual | ||||
M3-Plan | 24.4.yy/Saturday | |||
Actual |
What is Predictive Maintenance?
Predictive maintenance is condition-based maintenance that monitors the condition & performance of equipment to reduce the probability of failure.
Advantages of Predictive Maintenance:
- Improve asset reliability.
- Provide better product quality.
- Improve the condition of equipment, etc.
The basic requirements for good maintenance practices:
The following are the basic requirements for achieving good maintenance practices as;
- Good supervision of the maintenance department.
- Do the maintenance plan and schedule a consultation with the production department, electrical department, utility service department, etc., and prioritize the machine to be covered under maintenance.
- Maintenance personnel should be well-trained.
- SOP, standard, to be followed.
- Adequate stock of spares should be kept.
- A checklist, logbook, and maintenance register should be maintained.
- 5’S to be maintained.
- CLIT to be followed.
Free Templates / Formats of QM: we have published some free templates or formats related to Quality Management with manufacturing / industrial practical examples for better understanding and learning. if you have not yet read these free template articles/posts then, you could visit our “Template/Format” section. Thanks for reading…keep visiting techiequality.com
Useful Post:
Simple Moving Average Formula |Calculation |Excel Template |Example
MTBF and MTTR |Template |Format |Calculation | Manufacturing Example
AIAG VDA FMEA Key Changes | Overview | 7 Step FMEA |PFMEA |1st Edition 2019 | Training
5G Problem solving technique | Manufacturing Example |Free Template
More on TECHIEQUALITY